Welding is a critical process in many construction projects, and as a site engineer, understanding its fundamentals is crucial. While you might not be performing the welds yourself, you are responsible for ensuring that welding is executed correctly, safely, and according to specifications. This guide covers the essential aspects of welding that every site engineer should know.
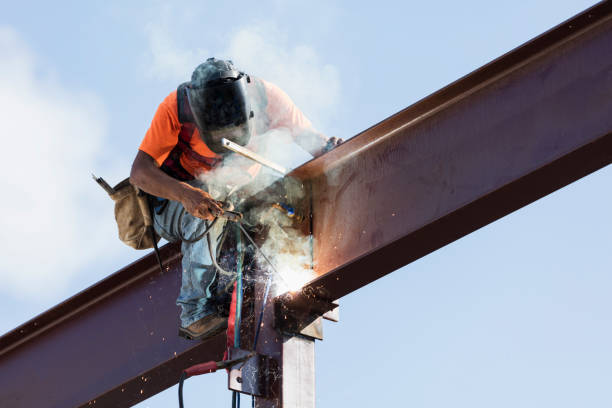
Why Site Engineers Need to Understand Welding
As a site engineer, you’re the bridge between design and execution. You’ll deal with:
- Reviewing Welding Procedures: Making sure that the welding procedures are appropriate and approved.
- Inspecting Welds: Identifying potential defects and verifying weld quality.
- Managing Welders: Ensuring welders are qualified and follow correct procedures.
- Troubleshooting Problems: Addressing issues that arise during welding operations.
- Safety Oversight: Enforcing safety protocols to prevent accidents.
- Coordination: Coordinating welding activities with other trades on site.
4 Types of Welding Explained: MIG vs TIG vs Stick vs Flux Core
Key Welding Processes for Construction
Several welding processes are commonly used in construction, each with its advantages and disadvantages:
- Shielded Metal Arc Welding (SMAW) / Stick Welding: A versatile and relatively inexpensive process that uses a coated electrode to create the weld. It’s suitable for various metals and thicknesses but can be slower and produce more slag. Site Engineer Relevance: Commonly used for repairs, field welds, and structural steel connections. Requires more skilled welders.
- Gas Metal Arc Welding (GMAW) / MIG Welding: Uses a continuously fed wire electrode and a shielding gas to protect the weld from contamination. Faster and easier to learn than SMAW, making it suitable for production welding. Site Engineer Relevance: Good for structural steel fabrication, sheet metal work, and pipelines. Often used in workshops and prefabrication.
- Flux-Cored Arc Welding (FCAW): Similar to GMAW, but the electrode contains a flux that provides shielding gas. It’s often used for welding thicker materials and in outdoor environments where wind can affect shielding gas. Site Engineer Relevance: Excellent for heavy structural steel, bridge construction, and applications where high deposition rates are needed.
- Gas Tungsten Arc Welding (GTAW) / TIG Welding: Uses a non-consumable tungsten electrode and a shielding gas. It produces high-quality welds with excellent control but is slower and requires more skill. Site Engineer Relevance: Used for critical welds requiring high precision, such as stainless steel or aluminum, and for root passes in pipe welding.
- Submerged Arc Welding (SAW): Uses a continuously fed wire electrode and a granular flux that covers the weld area. It’s a high-deposition-rate process suitable for long, continuous welds. Site Engineer Relevance: Often used in heavy fabrication, such as shipbuilding and large structural components.
Essential Welding Terminology for Site Engineers
- Weld Joint: The configuration of the parts being joined (e.g., butt joint, lap joint, fillet joint).
- Weld Bead: The metal deposited during a single pass of welding.
- Weld Pass: A single progression of welding along a joint. Multiple passes may be needed for thicker materials.
- Heat-Affected Zone (HAZ): The area of base metal that has been altered by the heat of welding. Its properties can be different from the original metal.
- Fusion Zone: The area where the base metal and filler metal have melted together.
- Slag: A non-metallic byproduct of welding that needs to be removed.
- Undercut: A groove melted into the base metal next to the weld bead. It weakens the joint.
- Porosity: Small voids or gas pockets within the weld metal.
- Incomplete Fusion: Lack of complete melting and joining between the weld metal and the base metal.
- Incomplete Penetration: Failure of the weld metal to fully penetrate the joint.
- Weld Procedure Specification (WPS): A document that describes the welding process, materials, and parameters to be used for a specific joint. Crucial for Site Engineers: Ensure these are approved and followed.
- Welder Qualification: Certification that a welder has demonstrated the ability to perform welds according to specific standards.
Inspecting Welds: What to Look For
Visual inspection is the first line of defense. Check for:
- Surface Defects: Cracks, porosity, undercut, overlap, and incomplete fusion.
- Weld Size and Profile: Verify that the weld meets the specified dimensions.
- Cleanliness: Ensure that slag and spatter have been removed.
- Alignment: Check for any distortion or misalignment of the parts.
Non-destructive testing (NDT) methods, such as radiographic testing (X-rays), ultrasonic testing (UT), magnetic particle testing (MT), and dye penetrant testing (PT), may be required for critical welds. Ensure NDT is performed by qualified personnel and that results are properly documented.
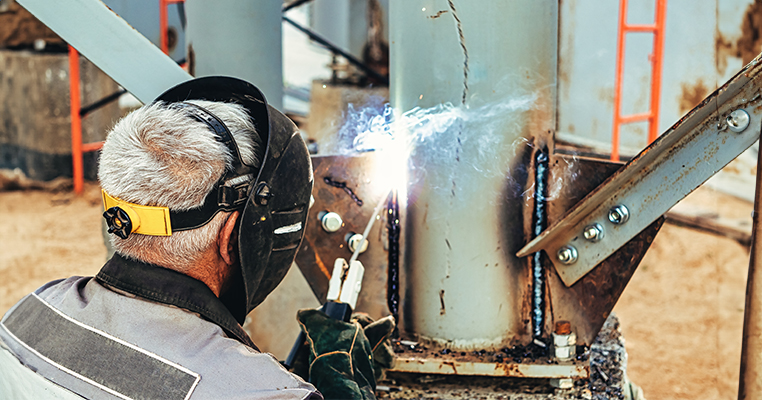
Safety First: Welding Hazards and Precautions
Welding poses several hazards:
- Arc Radiation: Can cause burns to the skin and eyes. Prevention: Use appropriate welding helmets and protective clothing.
- Fumes and Gases: Can be toxic and cause respiratory problems. Prevention: Ensure adequate ventilation and use respirators when necessary.
- Electric Shock: Can be fatal. Prevention: Use properly grounded equipment and avoid working in wet conditions.
- Fire and Explosions: Welding can ignite flammable materials. Prevention: Clear the work area of combustibles and have fire extinguishers readily available.
As a Site Engineer, you’re responsible for ensuring that all welders follow safety protocols and use appropriate personal protective equipment (PPE).
Recommendations for Further Learning
- The AWS Welding Handbook: A multi-volume series covering all aspects of welding, from fundamentals to advanced techniques. While it’s extensive, it’s an invaluable resource for any engineer involved in welding. Look for Volume 1 (Welding Science and Technology) and Volume 2 (Welding Processes).
Conclusion
Welding is a vital process in construction, and understanding its principles, terminology, and safety aspects is essential for site engineers. By familiarizing yourself with the information in this guide and pursuing further learning, you can confidently oversee welding operations on your projects, ensuring quality, safety, and compliance with specifications.